7 POINTS TO CHECK TO IMPROVE TABLET QUALITY
1. WORKING LENGTH OF THE PUNCH
The size of the punch is very important especially for rotary tablet presses because it plays a role in consistency in weight, hardness and thickness of the tablet. Therefore, they must be measured directly and the tolerance must not exceed 0.002 inches (0.0508 mm) on an operating station at upper and lower punches. The working length of the punch must be checked carefully during operation and checked on site on new punches when they are installed
2. DIE BORE WEAR
This point is often overlooked in the process of checking the operation of punches and dies because until there is a lack of efficiency and technical response, it prevents checking this wear. New machines like Punch & Die Condition Tester can help us measure and monitor punch and die wear. Die bore wear can cause tablet defects such as surface peeling, layer separation and edge overflow
3. PUNCH TIP WEAR AND CAMBER
The camber of the punch tip should be checked for “Hook” marks. The J-hook mark is characterized by the edge of the punch tip bending into the inner surface. This type of wear can cause surface peeling during tablet production. The punch tips should also be checked for excessive gaps as they are similar to die bore wear. And like die bore wear, this problem can be measured using a Punch & Die Condition Tester or by using an optical comparator. If using a traditional Panme micrometer, it will not be possible to accurately measure punch tip wear
Máy kiểm tra tình trạng chày cối
4. PUNCH COTTER KEY
This is a part of the tablet press, the punch cotter key can play an important role in the quality of the tablet. There are tips to check when they are worn out. If worn, they should be replaced, as when worn they can cause weight differences in tablets.
5. PRESSURE ROLLER
This is another checkpoint on the tablet press, the pressure roller need to be checked for “eccentricity” or also called concentricity check. Failure to check the wear of the roller can cause inconsistency in hardness and weight of the tablets. The concentricity can be checked by using a dial indicator tool attached to a metal rod and a magnetic base. The measurement is done by taking the average measurement to determine whether the wear of the roller is within the tolerance range.
Dial gauge used to check the concentricity of the punches
6. CAM WEAR AND TABLET DOSAGE
The cam should be checked for wear by eye or more carefully after removing it. The cam also needs to be checked and selected to have the appropriate tablet dosage depth. Incorrect dosage depth can lead to excessive product loss and tablet weight variation.
7. TABLET EJECTOR CAMERA
This checkpoint should be checked with a straight edge ruler. The edge of the ruler must be in contact with the tip of the punch and ensure that there is enough clearance for the tablet ejection process. Setting the tablet ejector cam at the appropriate height will reduce the problem of tablet edge chipping.
Checking the suggested areas on the machine and correcting any wear or defects is a very worthwhile step, as it will improve product quality and reduce punch and die costs due to wear and damage.
Another important thing is to build written inspection procedures to ensure that best practices are followed. Another important thing is that staff must carefully check whether the parts of the tablet press and punch and die are within the given tolerances and in good condition.
READ MORE
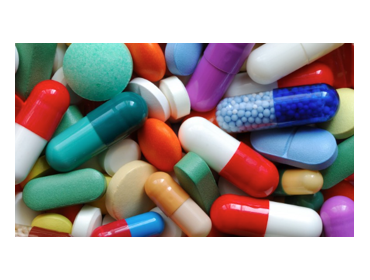
Selecting pharmaceutical machinery is a critical process that requires careful consideration to ensure compliance with regulatory requirements, product quality and operational efficiency.

In the ever-evolving landscape of pharmaceutical manufacturing, precision and efficiency take center stage. Our cutting-edge Auto Coating System revolutionizes the coating process, ensuring optimal product quality and streamlined operations. Let’s explore the key features that set our system apart:
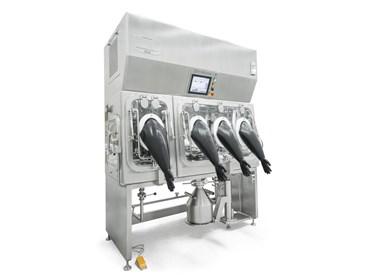
Tien Tuan is thrilled to unveil our latest innovation in pharmaceutical containment technology – the Dispensing Isolator.
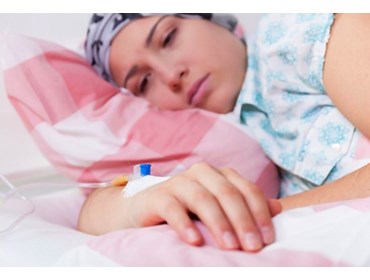
Some of challenges and typical benefits briefly of blister packing Fentanyl Citrate
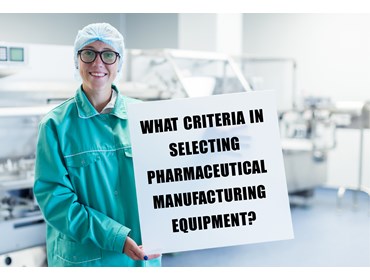
Selecting pharmaceutical equipment is a critical process that requires careful consideration of various factors:
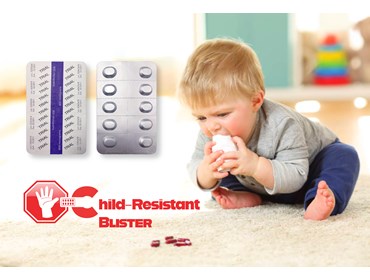
Child-resistant blister packaging is designed to prevent young children who may be curious and explore their environment from accessing and potentially ingesting harmful substances such as medications, yet remain relatively easy for adults to access.
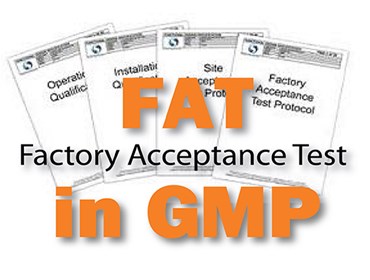
FAT and GMP: IMPORTANT LINKS IN THE INVESTMENT PROJECT FOR PHARMACEUTICAL PLANT DEVELOPMENT
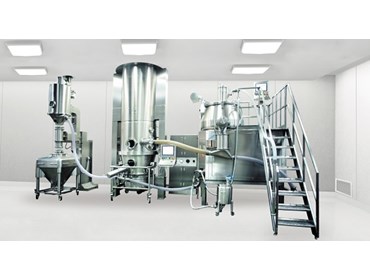
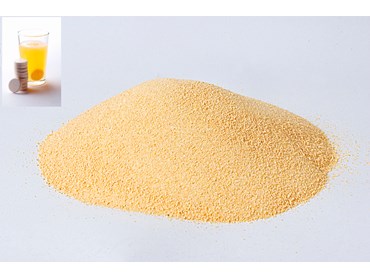
The wet granulation process in two separate steps is the most widely used technology and it is suitable for traditional drug mixing equipment such as Mixer & Granulator and Fluid-bed Dryer & Granulator.
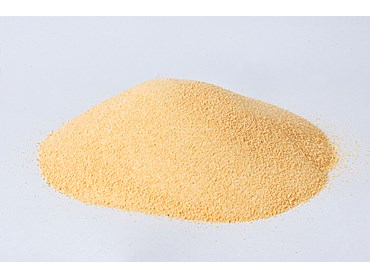
The one-step granulation process helps to create granules directly, by granulating acid and alkali granules together. Usually, water is used as a granulation solution, so the effervescent reaction must be controlled during the granulation process. Ethanol or propanol can also be used as a granulation solution, but then additional binders are needed to achieve the necessary cohesion. There are 2 types of equipment used to prepare effervescent tablets according to this technology
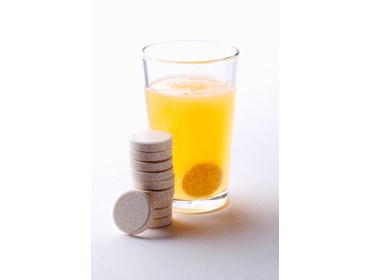
Effervescent tablets have the main advantage of being easy to use, especially effective for patients who are children. However, their production is more complicated than traditional tablets, especially the selection of technology and equipment.
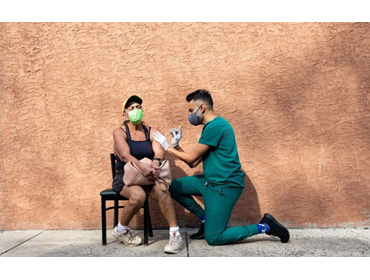
The effects of the new variant are difficult to announce accurately because unlike previous variants, Omicron mainly attacks young people who have better resistance.
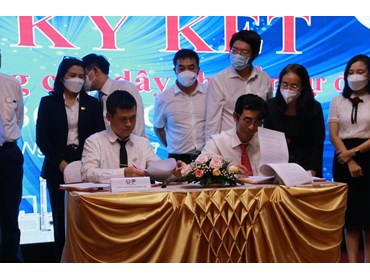
Signing ceremony for cooperation in supplying fully automatic blistering cartoning line according to GMP-EU standard for US PHARMA
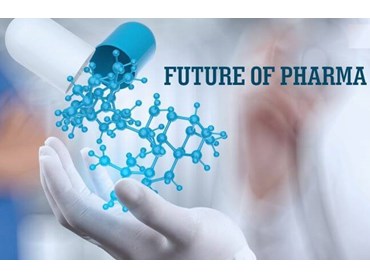
The Covid-19 pandemic has posed new challenges for pharmaceutical startups. What needs to be done to survive and develop, especially in this period. The StartUs Insight newspaper based on the analysis of “1745 famous pharmaceutical startups in 2020”, found the most outstanding startups. To turn challenges into opportunities, pharmaceutical companies have had “tips” for startups to survive the pandemic.
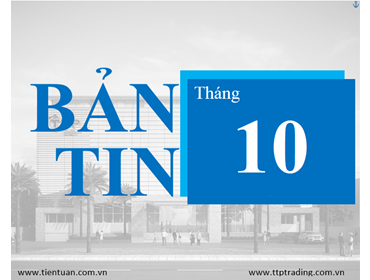
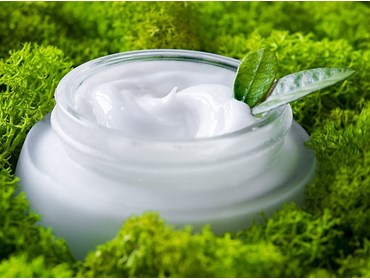
If you are interested in beauty, you must have heard of collagen skin care. Even many cosmetic companies have launched products that contain collagen, such as moisturizers, lotions, serums, etc.
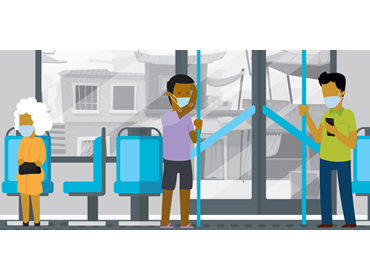
Ở một số nơi, khi số ca mắc #COVID-19 giảm xuống, một số biện pháp phòng chống dịch đang được gỡ bỏ...
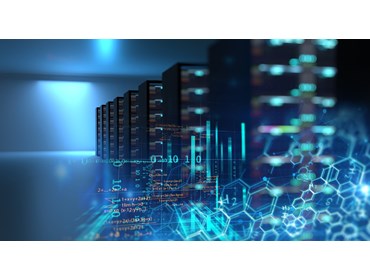
Ngành công nghiệp dược phẩm tuân theo các yêu cầu khắt khe nhất đối với quá trình sản xuất và thiết bị được sử dụng phải tuân thủ thực hành sản xuất tốt (GMP). Khi xu hướng phát triển thuốc thay đổi, các quy trình sản xuất cũng phải thay đổi, phần lớn trong số đó hiện có thể được tự động hóa...
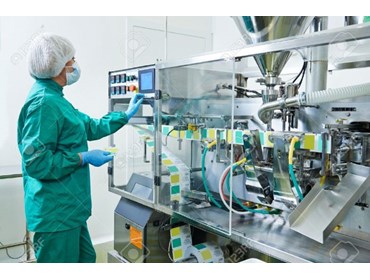
Cuộc khủng hoảng y tế COVID-19 mang lại những tác động và tiến bộ khoa học mạnh mẽ đồng thời cũng rút ra được những bài học kinh nghiệm quý báu cho các doanh nghiệp, tổ chức và các quốc gia trên thế giới:
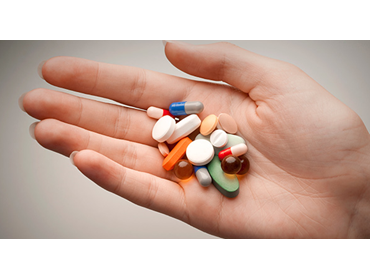
Tại Trung tâm chống dộc Bệnh viện Bạch Mai đã tiếp nhận rất nhiều trường hợp bị ngộ độc do lạm dụng thuốc hạ sốt paracetamol để chữa COVID-19. Do đó, người dân nên cẩn trọng trước các bài thuốc lan truyền không rõ nguồn gốc trên mạng xã hội, trước khi sử dụng bất kỳ loại thuốc nào cần xin ý kiến bác sĩ, không được tự ý sử dụng.
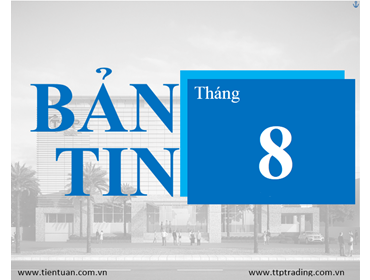
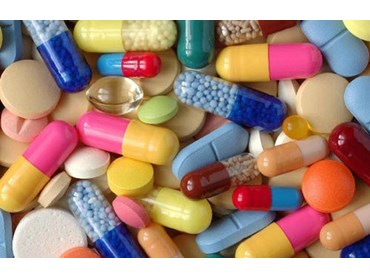
Từ ngày 1/8/2021 doanh nghiệp có thể tra cứu trạng thái chứng nhận xuất xứ mẫu D trên internet. Đồng thời các doanh nghiệp nhập khẩu các lô hàng thuốc, nguyên liệu làm thuốc nhập khẩu luồng đỏ phải xuất trình bản gốc giấy uỷ quyền, giấy phép lưu hành và phiếu kiểm nghiệm sản phẩm
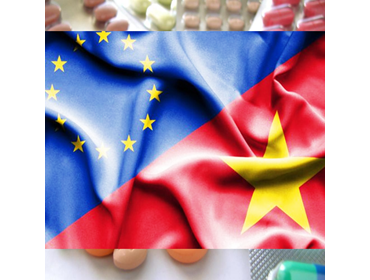
Hiệp định thương mại tự do Việt Nam - EU (EVFTA) có hiệu lực từ tháng 8/2020 mở ra nhiều cơ hội trong quan hệ đối tác toàn diện giữa hai bên. Tác động của EVFTA đến ngành dược phẩm đã có những kết quả dần rõ nét, đặc biệt là đối với các doanh nghiệp Châu Âu.
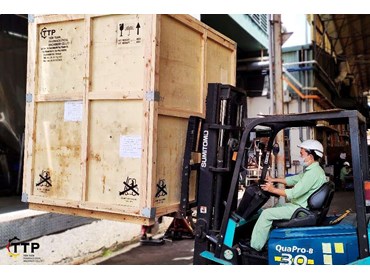
Việc duy trì sản xuất và giao hàng đúng hạn, giữ đúng cam kết với khách hàng là nỗ lực đáng ghi nhận, thể hiện uy tín, nội lực và sức cạnh tranh cao của Tiến Tuấn.
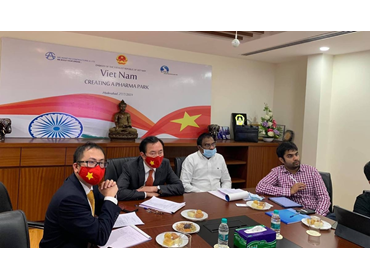
Theo Đại sứ quán Việt Nam tại Ấn Độ, đây là gợi ý được các ông lớn trong ngành dược phẩm Ấn Độ đưa ra trong buổi họp xúc tiến thương mại đầu tư do Đại sứ Việt Nam tại Ấn Độ - ông Phạm Sanh Châu chủ trì.